|
|
Examples of shear strengthening with: |
(a) |
closed (properly anchored) jackets |
(b) |
discrete strips anchored in the compression zone |
(c) |
open jackets. |
The option "Closed jacket" or "Open jacket"
is selected, depending on the type of strengthening system used.
Shear strengthening of columns where all four sides are accessible
is typically of the closed-type. Moreover, shear strengthening of
T-beams with mechanical anchorage systems that ensure perfect anchorage
of the FRP in the compression zone may be considered of the closed-type
too. This is the case, for instance, with the CarboShear elements,
if sufficient anchorage length is available through the slab. For
these particular elements, if the anchorage length is less than
300 mm, it is recommended to take a solution, calculated by linear
interpolation between "Closed jacket" and "Open jacket",
that is to run the programme for both cases and adopt the value
by linear interpolation. Consult also the technical datasheet and
design recommendation of this product.
Closed jackets or properly anchored strips are always preferable
compared with open jackets, as in the latter case the FRP is debonding
prematurely and is, therefore, of reduced effectiveness.
The external FRP reinforcement may be treated in analogy to the
internal steel (accepting that the FRP carries only normal stresses
in the principal FRP material direction), assuming that at the ultimate
limit state in shear (concrete diagonal tension) the FRP develops
an effective strain in the principal material direction, f,e
which is, in general, less than the tensile failure strain, fu.
The effective strain depends on the degree of FRP debonding when
the shear capacity of the RC is reached, that depends on the type
of anchorage (properly anchored FRP, e.g. closed jackets, versus
poorly anchored FRP, i.e. open jackets). Hence, the shear capacity
of a strengthened element may be calculated according to Eurocode
2.
Input:
Vfd is the contribution of FRP to the member's shear
capacity. Ef is the elastic modulus of FRP, b is the
width of the cross section, d is the static (or effective) depth,
is the angle between the principal
FRP fibre orientation and the longitudinal axis of the member, fd,e
is the design value of the effective FRP strain and rf is the FRP
reinforcement ratio, equal to (2tf/b)sin
for continuously bonded FRP of thickness tf, or (2tf/b)(bf/sf)
for FRP reinforcement in the form of strips or sheets of width bf
(perpendicular to the fibre orientation) at a spacing sf
(axis to axis of strips along the member axis).
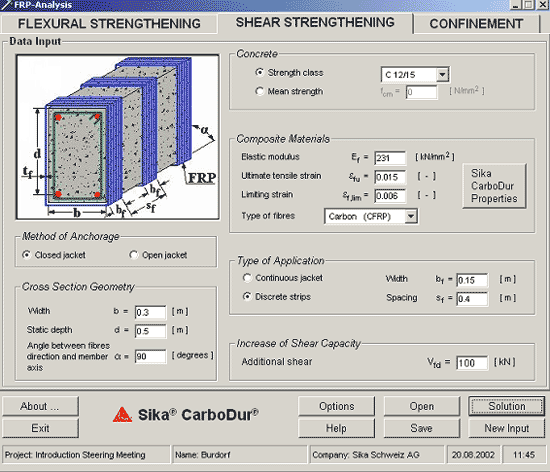
In the above, fcm is the mean compressive strength of
concrete in N/mm2, Ef is taken in kN/mm2,
k is a constant relating the characteristic to the mean value of
the effective FRP strain (default: k = 0.8) and f
is the FRP material safety factor. The f
factor depends on the type of FRP material as well as on the failure
mode governing shear design.
The first term (described in eqs. (1.3.3a), (1.3.3b) and (1.3.4)
in the help function) corresponds to FRP fracture (when the member's
shear capacity is reached), hence the use of f,f
(= 1.20 for CFRP, 1.25 for AFRP, 1.30 for GFRP), the second term
in eq. (1.3.3 of help function) corresponds to FRP debonding, hence
the use of f,b (= 1.30),
and the last term is taken (with f,l
= 1.25) if it is desired to limit the FRP strain in order to maintain
the integrity of concrete and secure activation of the aggregate
interlock mechanism. It should be noted that these FRP material
factors may be changed through "Options".
The thickness of FRP required to provide a shear
resistance equal to Vfd will be calculated.
After the input of the effective thickness of the
FRP - layer, the number of layers and the effective reinforcing
shear capacity can be calculated.
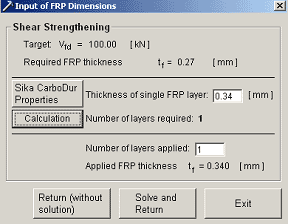
|